3D-Printed Homes: A Sustainable Construction Method on the Rise
The 3D-printed homes market is a relatively new approach to prefabricated housing that involves the use of 3D-printing technology with the potential to design out carbon from the construction industry. This technology uses automated robotics to build three-dimensional objects by adding layer upon layer of material and it has the potential to reduce manufacturing costs and increase the overall efficiency of home building.
Our figures show increasing investment in sustainable construction design innovation. In the last two years, we’ve seen over $140M invested in innovators emerging in 3D-printed buildings with considerable investments from venture capital, corporate and prop-tech investors.
Many innovators, such as Katerra and Juno, streamline the construction process and consider the entire building’s lifecycle from embedded emissions in materials, to building energy efficiency, through end-of-life or repurposing. Among these innovators working to bring 3D-printed methods to market is Mighty Buildings.
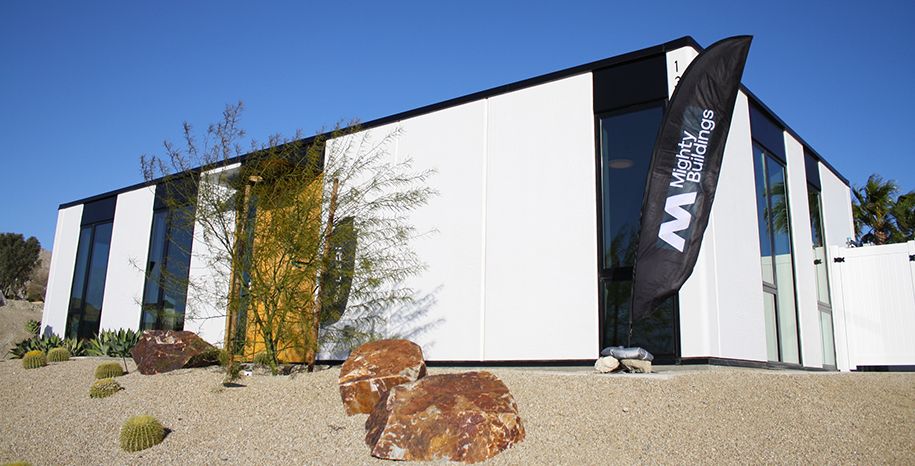
Mighty Buildings, founded in 2017 and based in Oakland, California, is a provider of Zero Net Energy (ZNE), prefabricated single-family homes manufactured using 3D-printing technology. A ZNE building is an energy-efficient structure that produces as much energy as it consumes over the course of a year, usually by incorporating renewable energy generation on-site.
Recently, the Mighty Buildings team invited Cleantech Group to view their latest project, a community of 3D-printed homes, with sustainable housing developer, Palari, in Desert Hot Springs, California.
Mighty Buildings’ homes are comprised of thermoset composite panels made from 60% recycled materials that are climate-resilient even to extreme weather such as hurricanes, earthquakes, flooding, etc. Design to completion can be as quick as 2-3 months, and homes can be ‘stitched’ in as little as one week.
The panels are stitched onsite, reinforced with load bearing steel, and the roof consists of 8-foot-long steel cassettes. Currently, the panels and cassettes are finished with drywall after install, however, Mighty Buildings aims to further reduce waste with panels that can be installed without the need for drywall. These are expected to be introduced to the market in the next couple of years.
Prefabricated bathroom and kitchen pods are readily stitched into the customizable layout of approximately 1,000 square feet with unique finishings. Sustainable designs include greywater reuse, solar panels, energy-efficient batteries, and high-insulation materials.
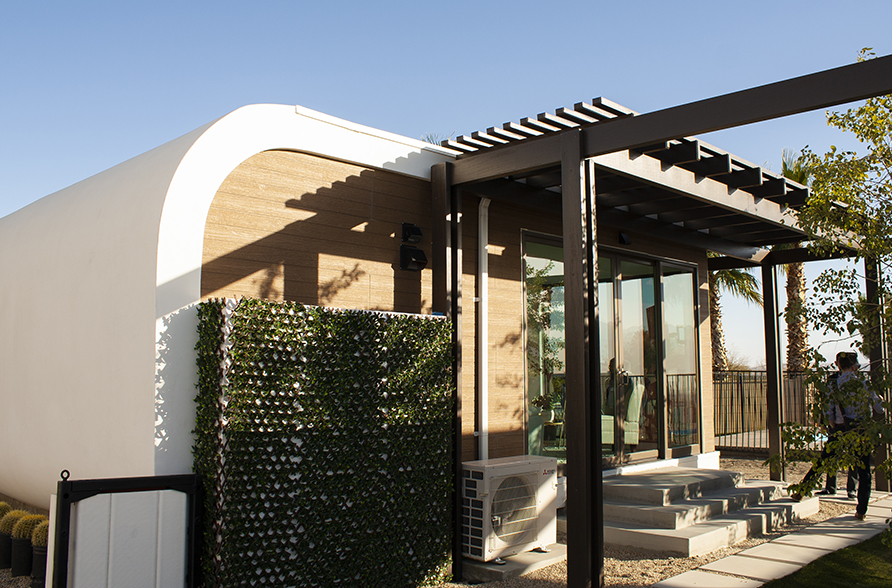
This innovation by Mighty Buildings is by no means premature and comes on the heels of the aftermath of the COVID-19 pandemic. Supply chain issues that were exaggerated by the COVID-19 pandemic continue to cause significant increases in home building prices while negatively impacting the quality of homes and construction timelines.
This is clearly a step in the right direction to relieve these supply chain challenges and reduce traditional labor costs by manufacturing homes in automated factories with 3D printers and robots that speed up the process.
The construction industry is projected to produce up to 2.2B tons of waste globally by 2025 with building materials estimated to make up half of that solid waste. Traditional building materials such as concrete and wood often require significantly large amounts of energy and resources to manufacture and transport and may not always be recyclable or biodegradable. The Mighty Buildings’ homes are constructed with near zero waste, and they reduce as much as 99% water usage when compared to traditional building methods.
Mighty Buildings also intends to expand into other markets to make their materials not only residentially available but also widely commercially available. However, public perception of these homes may be the biggest roadblock to achieving that goal.
While the 3D-printed homes market is still relatively new, there are other exciting innovators competing to bring their 3D-printed solutions to market as well. Some other key innovators in this space include:
- ICON, a developer of 3D-printing, robotics, and other advanced materials for construction. ICON announced they will build a community of 3D-printed homes in Georgetown, Texas in 2023.
- MOBBOT, a developer of 3D-printed concrete materials. Based in Switzerland, they recently participated in CER3N, a feasibility study for the construction of a 100km long collider.
- COBOD, a designer of 3D construction printers and automated processes. Based in Denmark, they partnered with Power2Build to develop Angola’s first 3D-printed home.
3D-printed homes have the potential to revolutionize construction and reduce the intensive carbon footprint of that industry. While not the current focus, this would eventually make housing more affordable and accessible, especially in areas with increasing housing costs.
If these innovators can show that their designs are safe, durable, and sustainable when compared to traditional homes, 3D-printing may no longer simply be a fun way for engineers and architects to model prospective projects, but a viable and sustainable construction building method.
While many remain skeptical of the safety and practicality of these homes, Mighty Buildings is evidence that continued exposure to 3D-printed buildings will allow more opportunity for the public to familiarize themselves with these durable, energy-efficient homes that can help usher in a net-zero energy future.
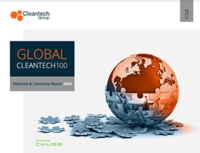