How Industrial Waste is Enabling Carbon Mineralization
There’s a lot of buzz around high-quality carbon capture technologies, but it seems like they’re always 10-20 years away from commercial scale. So, for now, we’ve had no choice but to rely on lower-quality and nature-based carbon capturing solutions. While these solutions are great options, they generally have some kind of impermanence associated with them. For example, planting a tree is a good solution, but when that tree dies or is burned, its stored carbon is released back into the environment.
The top emerging innovations to sequester carbon permanently include biochar, enhanced rock weathering, and carbon mineralization—the latter is the focus of this blog.
Carbon Mineralization
Carbon mineralization is a process that mimics the Earth’s primary carbon dioxide (CO2) regulation method. Earth naturally converts CO2 in the atmosphere into rocks or minerals over millions of years. In our oceans, even living beings sequester CO2 in their exoskeletons (e.g., shells, coral reefs, etc.) that is buried under the seafloor when they die, and that will take hundreds of millions of years to be recycled into the atmosphere.
The natural mineralization cycle is relatively simple; however, natural mineralization cannot keep up with the excess CO2 that humans have generated. Currently, natural mineralization can only sequester 0.7 GT of CO2 per year. Unfortunately, humans emit nearly 36 GT of excess CO2 emissions per year (IEA 2022).
While the process is relatively straightforward, it took researchers until about 20 years ago to understand the kinetics behind the reaction so that they could mimic it in a lab. Carbon mineralization traps CO2 into the crystal structure of carbonate minerals resulting in its permanent sequestration. This is conducted both in-situ and ex-situ manners.
For in-situ operations, CO2 and water are injected underground to create a calcium carbonate derivative that stores the CO2 when reacted with calcium-/magnesium-bearing minerals. In-situ operations are subject to environmental conditions, and gases and water can leak out of cracks in underground reservoirs.
Enter Greenore
Greenore, recently named an APAC Cleantech 25 company, is spun-out of Columbia University and founded by Xiaozhou (Sean) Zhou who was researching sustainable ironmaking, and carbon sequestration and utilization processes. Greenore converts iron and steel making by-product, slag, into chemical products (calcium/magnesium carbonate, iron oxide, silica, alumina, and rare earth concentrate), while consuming CO2 as a reactant. Greenore has developed a catalyst that mimics the Earth’s natural mineralization process without its time constraint.
Greenore achieves this via ex-situ mineralization, a process that mimics in-situ mineralization above ground. Due to its high availability, alkaline industrial solid wastes can be utilized for ex-situ mineralization such as steel slag, iron slag, mine tailings, cement waste, and more. These materials are generally rich in calcium-/magnesium-based minerals which can sequester CO2 quicker than other natural weathering processes.
Principle of Greenore’s Carbon Mineralization Pathway
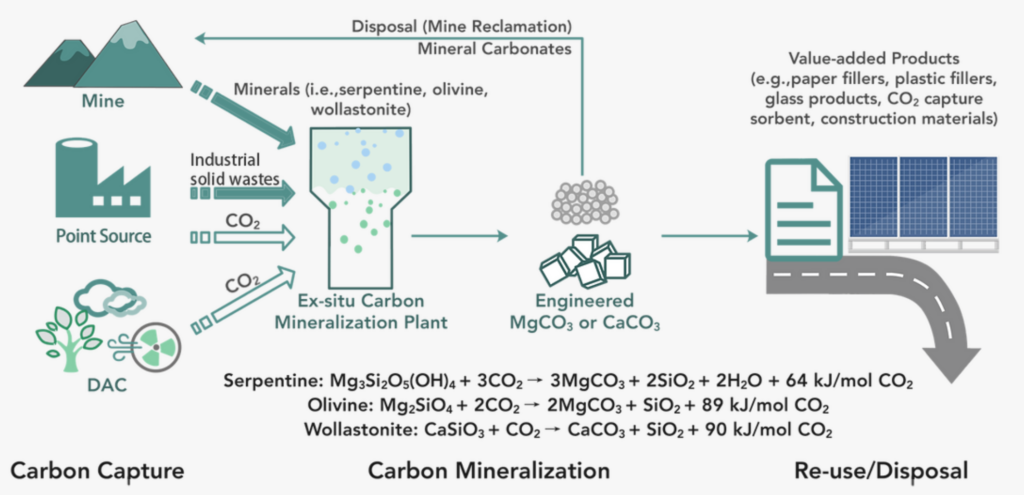
According to Greenore, decarbonizing steel production and reducing its waste from production is a global issue as it accounts for 7% of the anthropogenic carbon emissions. China has an estimated 660M tons of CO2 sequestration potential capacity from legacy slag waste, where the UK has an estimated 190M tons of CO2 sequestration capacity. This waste is generally discarded in landfills where it poses environmental hazards. Slag-based carbon mineralization not only reduces CO2 emissions, but also employs waste utilization making it a lucrative opportunity for engagement.
Greenore reduces its overhead costs by utilizing industrial waste as its feedstock, and its carbon capture and utilization (CCU) solutions are flexible with the range and scope of the CO2 sources. The carbon can be sourced from ambient air, flue gas, etc., and can be sequestered via any CCU technology like point source or direct air capture (DAC).
Greenore’s process converts up to 0.2-0.25 tons of CO2 per ton of waste slag or 1,248 kg of CO2 per 1,000 kg of steel slag processed with minimal reagents and chemicals utilized and recycled. Once processed, the sequestered CO2 can be used as feedstock for cement, papermaking, paints, 3D printing, plastics, etc.
Greenore’s ex-situ process is modularized but can process relatively large volumes of slag waste. A typical module can process 50k tons of slag per year or 10k tons of CO2. A module can be set up on a “Build, Own, Operate” model in centralized markets, but licensing is also adopted for regions where markets are still growing. This has attracted partnerships with big players like POSCO, SD Steel, Harsco, and more.
In partnership with Baotou Steel, a steel producer, Greenore entered its first commercial scale of a carbon mineralization plant based on slag. The plant successfully produced its first batch of calcium carbonate in July 2023. In January, Greenore partnered with TBM, a developer of a recyclable alternative to plastic and paper, LIMEX. Greenore’s CCU calcium carbonate will be integrated into TBM’s LIMEX material.
Forward looking, Greenore isn’t stopping at slag. In February, Greenore completed a Series A round led by Amperex Technology Limited (ATL) to explore battery recycling. “Fundamentally, the chemistry of utilizing carbonic acid can be applied to lithium battery recycling,” said Zhou.
As governments, industries, and research institutions collaborate to further develop and deploy carbon mineralization technologies, innovators like Greenore are paving the way for carbon mineralization to be commercially available. And while this technology may not be as cost competitive as other CDR methods, it’s a permanent carbon sequestration pathway that is not only a waste management solution but can even be utilized in valuable products. However, realizing this potential will require continued embrace of innovation, significant investment in its infrastructure, and collaboration across sectors beyond iron and steel slag waste.