Biodegradable Bioplastics: Decarbonizing a “Throw-Away Economy” Built on Cheap and Durable Plastics
Global Infrastructure that Relies on Plastics
The global utilization of plastics in our everyday lives has made it seemingly impossible to imagine life without it. A majority of plastics are used in packaging, especially single use, but also in automotive, textiles, and engineering and industrial applications.
Plastics gained widespread popularity due to their durability, flexibility, and cost-effectiveness. So, it should come as no surprise that in 2023, the global plastics market was valued at a staggering $712B and is anticipated to climb to well over $1T by 2033 (Statista 2024). This market growth is an astounding achievement but is also cause for significant concern.
Because most conventional plastics are non-biodegradable, they can shed micro-/nano-plastic particles when discarded. These harm local environments, contaminate waterways, and cause health issues.
By 2040, global GHG emissions from plastics production, use, and disposal will rise from 1.9B tons in 2019 to 3.1B tons of CO2 emissions—an over 60% increase (Systemiq 2023). Annual plastics production will top 1.2B tons by 2060, doubling production and tripling waste, that would strain even the most developed recycling infrastructures (OCED 2022).
Ironically, Plastics Can Solve the Plastics Crisis
Biobased plastics and alternatives (hereinafter referred to as bioplastics) are materials derived from biomass, typically waste or lab-grown, and are intended to replace conventional plastics with a similar or identical function even if they are not an exact bio-derived alternative at the molecular level.
For those concerned about availability of biomass supply, countries have begun to build out their biomass supply chains. In March, the U.S. Department of Agriculture released its strategy to “boost biomass supply chain resiliency for domestic biobased product manufacturing, while also advancing environmental sustainability and market opportunities for small- and mid-sized producers.” (USDA)
Bioplastics exist for nearly every conventional plastic product and its respective application. In fact, bioplastics like PLA/PHA are in commercial production with technology readiness level (TRL) 8-9. By 2028, PLA and PHA production will increase to 3.2M tons and 1M tons, respectively (European Bioplastics 2023).
Emerging innovation in bioplastics production valorizes organic waste streams, thereby reducing overhead costs from feedstock sourcing compared to other production methods like growing microbes for PHA. Bioplastics can reduce a product’s carbon footprint by 40-70% (CE Delft), and naturally biodegradable bioplastics won’t shed micro-/nano-plastics when breaking down in natural environments.
Materials derived from biomass do not equate to biodegradability, and vice-versa. Thus, there are biomaterials that are not biodegradable. And there exist conventional plastics that are industrially compostable or biodegradable. Naturally biodegradable means a product is compostable at home whereas industrially biodegradable/compostable means a product must be sent to a processing facility to be processed.
Emerging innovators are tackling this biodegradability issue, especially for single use, to curb waste. For example, New Zealand-based Sleaktek is a developer of biodegradable biopolymers to replace single-use plastics derived from organic waste that are compatible with most production lines. Its materials actually improve the soil nutrients of the environment in which it breaks down. Nohbo developed water-soluble biofilms for single-use cosmetics applications.
France-based CARBIOS developed an enzymatic solution to make PLA home-compostable or naturally biodegradable with a TRL of 9. It was recently approved by the U.S. Food and Drug Administration to be a safe food contact substance.
Drop-in solutions allow vertical integration of bioplastics into existing production lines. Technical University of Denmark spin-out, Kvasir Technologies, is a producer of bioplastics, but also biofuels, biochar, and other products from non-food lignocellulosic waste. It recently raised a $3.2M Seed to build a pilot facility in Denmark.
There are also mixed-source bioplastic and petro-based plastics innovators for engineering and industrial applications where 100% bioplastics may not be suitable to avoid mechanical risks. Evoco has won partnerships with major brand owners by blending 80% biofoam with conventional plastics, relieving durability concerns associated with bioplastics. Texas-based EPSilyte produces biodegradable and recyclable bioPE.
Bans on Plastics Have Good Intentions, But Are They Harming Innovation?
Over 100 countries are phasing out and disincentivizing the production of conventional plastics, generally targeting single use, or requiring reduction of its use in plastics for durable plastics as social and environmental justice advocates call for action. For example, the U.S. has set a target to replace 90% of plastics with biomaterials in the next 20 years. The EU Policy Manifesto urges for support of biomaterials while encouraging stricter regulation of conventional plastics. And The Board of Investment of Thailand offers a range of non-tax and tax incentives to bioplastics manufacturers.
But bioplastics are being grouped into plastic bans. This may be because the first generations of bioplastics (PLA, PHA, bioPE, etc.) shed micro-/nano-plastics, they were typically only industrially biodegradable, and harmed recycling infrastructure. This led policymakers to form the same attitudes toward bioplastics as they do conventional plastics.
Misconceptions remain in the policy framework in countries like those in the EU with regards to land-use, environmental impact, contamination of waste streams and biodegradability (European Bioplastics 2023). Policy fails to recognize the positive impact that bioplastics have over conventional plastics. It limits bioplastics innovators with its overly cautious views, preventing the switch to biobased products and stunting innovation across the biomaterials landscape—not just bioplastics.
Even broader, this led to a culture of marketing bioplastics technology without mention of ‘bioplastic’ that has resulted in a confusing landscape for consumers, producers, and policymakers. Innovators are worried that their solutions will be banned from sale if it is revealed that their solution were to be considered a plastic. Or that consumers will take preference to products that omit mention of bioplastic. As such, innovators are marketing ‘biopolymers’, ‘biomaterials’, ‘plastic alternatives’, etc., as part of their push to introduce these materials to the market.
Of the 400M tons of plastic produced in 2023, only 0.5% of production were bioplastics. And while the bioplastics production capacity is anticipated to grow from 2.18M to 7.43M tons from 2023 to 2028, it would still only account for less than 2% of total plastics produced in 2023 (European Commission 2023).
Plastics Aren’t Going Anywhere
Despite the growing interest in bioplastics, it’s crucial to recognize that conventional plastics are deeply entrenched in our society and economy. The infrastructure built around the production, distribution, and disposal of plastics is extensive and not easily replaced or reconfigured. Therefore, while efforts to reduce plastic consumption and transition to more sustainable materials are essential, it’s unrealistic to expect plastics to disappear entirely.
There are non-plastic alternatives (i.e., wood, metal, composites, etc.), but these are unlikely to ever compete with the cheap and durable plastics we all know (think of those paper straws that quickly lose their structure before one can finish one’s drink that leaves a bad taste in consumer’s mouths).
Bioplastics are the most efficient solution to avoid an entire infrastructure overhaul.
There’s still a significant gap between bioplastics demand potential, availability of supply, and production capacity. As consumer attitudes and rapidly changing legislation continue to drive sustainability, investing in bioplastics may not only be financially rewarding but crucial to addressing the environmental challenges posed by conventional plastics. Nearly the entire plastics market remains untapped (99.5%), presenting a lucrative opportunity for investors to capitalize on bioplastics disrupting an enormous market.
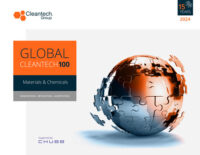