Cell-Free Biomanufacturing: Decentralized Approach for Fuels & Chemicals Synthesis
Chemicals manufacturing consumes approximately 10% of fossil fuels produced globally and expensive heavy metal or rare earth catalysts, the latter known to be increasingly expensive due to limited supply availability. While chemicals production via fossil fuels is successful, over 935 Mt were produced globally in 2022 or approximately 1.3 tons of CO2 produced per ton of primary chemicals, e.g., ethylene, (IEA 2023).
As of 2024, the globe is not on track to meet net-zero emissions by 2050. Both the private and public sectors will need to embrace employing more uptake of innovation and sustainable practices. There’s a significant need to adopt biological solutions as consumer attitudes and legislation support more sustainable practices, especially commodity chemicals, e.g., plastics, agrochemicals, textiles, etc.
Cell-free biomanufacturing enables commercial ventures as a decentralized biomanufacturing approach for bioactive molecules. Its systems can be easily ramped up or down according to demand for lab to commercial scale projects. Cell-free biomanufacturing utilizes the biomachinery present in a cell without needing to sustain life within. This results in highly adaptable systems that can perform in a range of testing and production schemes— removing the time-constraining growth cycles, homeostatic considerations, and limited adaptability associated with traditional biomanufacturing.
Cell-free systems reduce the timeline for chemicals discovery, consume less resources, improve process efficiency, and reduce biomanufacturing production costs at little-to-no upfront capital expenditure required to adopt — simply licensing. As a result, chemicals manufacturers can save millions per year with just small efficiency increases with process optimization schemes and the use of enzymes, i.e., biocatalysts. These biocatalysts are shelf-stable for months to years. What’s more, biocatalysts are continuously functional for weeks or months without regular decommissioning of bioreactors, saving chemicals plants time and money on maintenance.
But cell-free systems aren’t new and have been used in academic and industrial settings for a long time. The real innovation is the combination of artificial intelligence and/or machine learning (AI/ML) and extensive genomic libraries for digital simulation of reaction conditions. These genomic libraries keep track of DNA/RNA expressions needed to create enzymes with specific functions. Its functions are fine-tuned according to the customer’s specific requirements. Ideal conditions are determined within just hours as opposed to weeks or months and physical validation proceeds.
Innovators with the capability will then manufacture the desired product for their customer. Where demand is strong enough, a customer may choose to build its own plant or license technology at their existing facility. These cell-free biocatalysts are drop-in solutions that are durable, scalable, and highly performant.
Innovators to Watch
Enginzyme, a 2023 Global Cleantech 100 winner, reports reductions of 40% depreciation, 40% manufacturing cost, 70% energy consumption, and 40% raw materials consumption. Founded in 2014 by Karim Engelmark Cassimjee, Enginzyme has raised over $39M from ALMI Invest, Sofinnova Partners and more. Its systems seek to mimic chemical transformations found in nature, but it also has the capability to discover new enzymes to handle man-made processes, like for plastics. Currently, Enginzyme has reached commercial-scale demonstration and is manufacturing enzymes in-house. It has secured partnerships with major players like Terra Pak to develop sustainable packaging solutions.
FabricNano uses bioinformatics and formulation to optimize the binding of enzymes to rigid materials via its Immobilization Engineering™ platform. FabricNano uses this platform to select the right enzyme from nature and craft the corresponding formulation to encourage immobilization on rigid materials. They engineer the surface of the enzyme rather than the active site, such that enzymes interact optimally with external stimuli. Founded by Grant Aarons in 2018, the company raised over $12.5M from Atomico, Entrepreneur First, and others. In a first-of-its-kind partnership, Veolia and FabricNano use enzymes to remove carbon dioxide with enhanced rock weathering.
Solugen manufactures biobased chemicals using custom enzymes. Sustainable feedstocks are fed into a cell-free enzyme oxidation reactor that performs chemical transformations that are highly efficient with low energy input. They use dextrose (sugar) and convert captured carbon into useful products like building materials and formaldehyde-free resins. Founded in 2016, Solugen has raised over $612M from the U.S. Department of Energy, Lowercarbon Capital, Temasek, and others. They began construction of their Bioforge Marshall facility in Minnesota (U.S.) for large-scale chemical manufacturing. Solugen has partnered with major corporates like ADM.
Ginkgo Bioworks, a synthetic biology company with over $789M of capital raised, has partnered with cell-free innovators. Recently, FabricNano and Ginkgo Bioworks partnered to develop a range of enzymes for industrial process conditions. Ginkgo has also partnered with ZYMtronix to industrialize cell-free biomanufacturing.
What’s Next?
Major countries will need to invest in their own infrastructure to build bioeconomy supply chains or risk significant competition with imports, e.g., the U.S. Bioeconomy was valued at $950B in 2022, but China’s bioeconomy has grown to $380B where cheap labor and supply out-competes U.S. sellers (Forbes). The U.S. and China are leaders in cell-free synthetic biology with the U.S. investing significantly in research and commercialization of cell-free systems. In 2024, the U.S. National Science Foundation launched Advancing Cell-Free Systems Toward Increased Range of Use-Inspired Applications (CFIRE), a $40M funding program to accelerate cell-free systems in academia and industry.
Chemicals manufacturers should leverage these technologies in multiple tranches as it de-risks:
1) co-developing products or synthesis pathways or
2) ramping up to build, own, and operate where demand supports economies of scale.
Innovators seek to decarbonize the entire $5T chemicals industry beginning with commodity chemicals. Industries with informed consumers, e.g., fashion, or tolerance for green premiums, will see a near-term pull-through effect on demand for cell-free biomanufacturing. And we’re approximately five years away from cell-free systems disrupting industrial chemicals manufacturing practices.
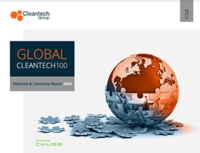