Cracking Ammonia: Dissociation and Fuel Innovation
Ammonia is often touted as the fuel of the future. It is gaseous at room temperature but can be liquefied under low pressure enabling its storage, while production requires hydrogen and nitrogen, unlike methanol which requires carbon. There is already 200 million tons per year of ammonia production which enables its wide distribution.
However, direct use of ammonia comes with challenges. For instance, combustion results in the production of nitrogen oxides (NOx) which are potent greenhouse gases and a health concern.
Ammonia cracking, the dissociation of ammonia into hydrogen and nitrogen, broadens potential applications for ammonia as an energy carrier and fuel. These include applications in:
- Energy: Production of hydrogen in PEM fuel cells, which have high efficiency and flexible operational ranges
- Transportation: Cracking enables use of hydrogen in engines; partial cracking can enable retrofits
- Industry: Cracking can provide a supply of hydrogen for industrial processes, e.g., direct reduction of iron ore.
How to Crack Ammonia
Traditional thermal cracking takes place at relatively high temperatures (up to 900°C) in a reactor with a catalyst. Heat required for the process is achieved by burning fossil fuels (directly or indirectly).
Depending on the application, the produced hydrogen may need to be purified using gas separation, e.g., pressure swing adsorption. The process is energy-intensive and equipment needs be designed to cope with high temperatures. The traditional process is not well suited to small scale which presents a barrier to use, especially where high temperature heat isn’t readily available.
A Growing Interest in Ammonia Cracking Innovation
Demand for alternative fuels and energy transportation, along with technological gaps, are fuelling interest in ammonia cracking innovations with venture money and corporate engagement increasing.
- Full cracking enables the use of hydrogen in fuel cells or industrial applications. Amogy has demonstrated significant traction in this space with a low temperature catalyst that achieves high conversion. Amogy closed a $140M Series B round earlier in 2023, with backers including Aramco Ventures, Mitsubishi Corporation, Mitsubishi Heavy Industries and Synergy Marine. The cracking system has already been demonstrated in tractors and trucks and the technology is set to be deployed in cargo ships and for remote power applications.
- Partial cracking enables the use of a hydrogen/ammonia mix in engines, enabling retrofit and/or use in harsh environments. The technology is under development by Sunborne Systems which was formed as joint venture between Science and Technology Facilities Council (STFC), Reaction Engines and Kiko Ventures in 2022. Another start-up, Ammonigy, has tested their technology in vehicles and small boats.
- Photocatalytic reforming uses electrical energy to power LEDs and provide energy for dissociation of ammonia, increasing efficiency at scale. Photocatalytic reforming catalysts have been successfully tested by Syzygy Plasmonics and a reactor is expected to be deployed at LOTTE Chemical in South Korean by the end of 2023.
- Catalytic membrane reactors separate hydrogen as it’s formed, avoiding the need for downstream separation. Catalytic membrane reactors are reaching pilot scale. The technology is under demonstration with incumbents including Fortescue Future Industries. Meanwhile, a recent spinout from Bettergy, Ammogenix expects to deploy small-to-medium-scale units for hydrogen fuelling stations beginning in 2025.
- Built-in absorbent columns separate hydrogen from the product gas. Oxgrin is part of a consortium which received £2.7M in the Clean Maritime Demonstration Competition in 2021 to develop a hybrid green ammonia marine propulsion system.
- Selective ammonia oxidation reacts residual NH3 with oxygen, purifying the product gas. The technology was developed by Rencat and then acquired by Alfalaval in 2022.
An Ammonia-Fuelled Future Ahead?
New approaches to ammonia cracking are helping to bridge the innovation gap. Ammonia cracking at lower temperatures with new catalysts can improve efficiencies, reduce equipment specification needs, and enable the integration of purification steps reducing capital equipment requirements. Application of photocatalysis promises significant efficiency gains. However, many of the technologies are yet to be commercially proven. The demand for ammonia cracking technologies is tied to the success of low carbon/green ammonia production, where round efficiencies and cost reduction are needed to achieve competitiveness with other developing solutions.
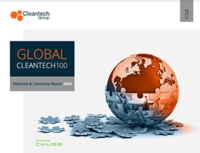