Decarbonizing the Chemical Industry: The Role of CO2 Electrolysis
The chemical industry is a significant contributor to global CO2 emissions, accounting for approximately 3% of total emissions. Key chemicals produced in the sector—such as ethylene, methanol, and propylene—are essential for industries ranging from plastics and textiles to energy. As the global focus on reducing emissions intensifies, the chemical sector faces increasing pressure to find more sustainable ways to produce these key chemicals.
While biobased alternatives offer a short-term solution, they are constrained by the limited availability of feedstocks, which could make scaling up challenging. As such, alternative routes to chemical production—such as CO2 electrolysis—are receiving increasing attention.
In recent years, the chemical industry has explored methods to use CO2 as a feedstock for producing valuable chemicals. Traditional processes typically combine CO2 with hydrogen to produce syngas (a mixture of carbon monoxide and hydrogen), which is then used to produce methanol and other chemicals. However, these methods face several challenges in terms of efficiency and cost.
CO2 Electrolysis and potential for process integration
CO2 electrolysis involves applying an electric current to CO2 in an electrolyzer, where the CO2 is reduced into products such as carbon monoxide (CO), which is used for production of syngas and derivatives. The approach offers a more direct and potentially energy-efficient conversion process compared to conventional methods. However, it is also competitive with other approaches including plasma processing.
Figure: Dioxycle – electrolyser cell
Co-electrolysis, which uses both CO2 and water (H2O) as feedstocks, expands the potential products from the process, allowing for the direct production of chemicals like methanol and ethylene. By integrating CO2 and water in a single process, co-electrolysis can produce a range of valuable chemicals within a single electrolyzer system, offering greater flexibility and scalability.
Key Applications for CO2 Electrolysis
Ethylene is one of the most widely used chemicals in the plastics and textiles industries. Dioxycle is developing modular electrolyzer systems capable of directly converting CO2 into ethylene. Dioxcyle raised $17M in 2023 to develop a demonstrator plant.
Methanol and formic acid are important chemicals used in energy storage, pharmaceuticals, and a variety of industrial applications. Companies including Oxylum and OCO Chem are actively developing CO2 electrolysis technologies to produce methanol and formic acid, with pilot projects underway.
Monoethylene glycol (MEG) and purified terephthalic acid (PTS) are key components in the production of polyester, widely used in textiles and packaging. Fairbrics raised equity funding in 2022 and is currently engaged in the EU-funded. THREADING-CO2 project which aims to deploy a one ton/day pilot plant by 2026
Sustainable Aviation Fuel (SAF) or specifically eJet, benefits from strong policy tailwinds including EU blending mandates. Innovators including Twelve and Air Company are looking to leverage CO2 electrolysis in production pathways. Twelve raised $600M (equity and project finance) in 2024 with a large- scale plant expected to be operational in 2025
Looking forward, Scaling Challenges and the Role of Policy
While CO2 electrolysis and co-electrolysis hold significant potential, these technologies remain in the various stages of development. Challenges include the cost of renewable energy and electrolyzers, which remain relatively high. Achieving cost reductions and improvements in efficiency will be key to their widespread adoption.
Long term availability of accessible CO2 feedstock could present an additional challenge. While point-source capture is currently the primary source, the future scalability of CO2 electrolysis may depend on expanding the availability of CO2. This could necessitate the use of Direct Air Capture (DAC) technologies which are significantly more expensive than point-source capture.
Continued policy support will likely be required to overcome these barriers. For example, tax credits like the U.S. 45Q (for carbon capture and utilization) and 45V (for clean hydrogen production) can incentivize the development of CO2 electrolysis technologies by lowering their cost. Similar policies in other regions will be critical in encouraging innovation and driving the cost reductions necessary to make CO2 electrolysis a viable solution at scale.
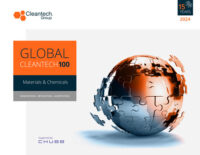