Hydrogen: A Fuel Carrier for Heavy-Duty Commercial Land, Maritime and Aviation Vehicles, and Energy Storage
In 2021, 98% of hydrogen was produced from fossil fuels—global emissions reached over 900 Mt of carbon dioxide amounting to 2.5% of all energy-related CO2 emissions. This heavy carbon-emitting industry is driven largely by the need for better working solutions for grid storage, steel and fertilizer production, and EVs, namely commercial heavy-duty, maritime vehicles and aviation.
Increased penetration of low-carbon hydrogen could play a significant role in industrial grid-load shifting and heavy-industry decarbonization. Low-carbon hydrogen (hydrogen with up to 80% carbon emissions reduction) could displace 94 Mt of grey hydrogen currently used for methanol and ammonia production.
Policy incentives, including tax breaks and other financial incentives, are likely to boost low carbon hydrogen production. We’ve seen global participation in the development of hydrogen infrastructure with Australia, the EU and the U.S. being the key main players:
- The U.S., under the Inflation Reduction Act (IRA), has implemented tax credits and has committed $8B toward the development of hydrogen production centers and infrastructure
- The EU announced plans for the Hydrogen Bank that supports contracting low carbon hydrogen and the development of the hydrogen value chain
Government-backed funding instruments such as auctions and contracts for difference (CfDs) are emerging alongside purchasing and offtake agreements, which will help make projects more bankable. Additionally, carbon pricing in some geographies will help fuel switching away from fossil fuels.
Low-carbon hydrogen production costs need to decline significantly from the current levels of $3-$7.5/kg to below $1/kg to be able to compete with hydrogen produced from fossil fuel, which are already priced at below $1/kg in some geographies depending on the price of natural gas or coal. Meanwhile, there is currently no merchant market for hydrogen so obtaining accurate price levels is difficult.
Getting the low carbon hydrogen price point to a fuel switching price point is likely only to occur faster in locations like Australia, where renewable energy is abundant. Meanwhile, global participation in building out the hydrogen value chain is required as there is plenty of skepticism over whether the hydrogen industry can attract the $80-$300B required to build the necessary infrastructure for production, storage, and especially distribution, by 2030.
Storage and Distribution—Innovation Supporting the Hydrogen Economy
Hydrogen transportation and storage is currently the weakest link in the value chain and although there are a variety of technologies available, most are plagued with financial or technical challenges, or both. Midstream costs can add up to 50% to the hydrogen landed costs.
The least expensive hydrogen storage option is underground salt caverns. These are relatively abundant and do not require much maintenance (e.g., Engie, Corre Energy), however many are currently still in use for natural gas storage.
Where caverns are unavailable, the most economical approach for the hydrogen economy will require hydrogen production near the industrial load centers. But there are many technical barriers that persist.
First, storing hydrogen as a compressed gas requires increased pressures (up to 700 bar) and/or cryogenic temperatures (-253°C). The necessary equipment required for pressurized tanks and refrigerators are expensive. Further, boil-off of hydrogen when using liquid hydrogen for transportation can lead to up to 5% losses per day.
Transporting hydrogen in pipelines (with an 80% natural gas blend) is the cheapest option for transportation. But hydrogen is corrosive to steel pipes and causes them to fail over time, i.e., hydrogen embrittlement, causing issues in pipeline distribution. Innovators like Oceanit and Smart Pipe are developing solutions to retrofit existing natural gas pipelines to prevent embrittlement by applying a coating or pipe-inside-a-pipe.
Storing hydrogen in the form of ammonia, methanol or formic acid is also attractive since the necessary infrastructure is mostly built (Ballard and Element 1). Hydrogen may also be stored in a liquid organic hydrogen carrier (LOHC), carbon-based carrier (EkarriH2 project supported by Tecnalia and Hydrogenious). LOHCs generally use toxic toluene-based oils or ionic liquids to carry hydrogen from production to end application. HySiLabs has developed an inorganic liquid hydrogen carrier using silicon hydride, instead of carbon-based.
MAHYTEC and Safe Hydrogen are using metal hydrides for hydrogen storage, i.e., magnesium hydride (MgH2). Electriq Global uses potassium borohydride (KBH4), a powdered solid. Storing hydrogen as a solid allows it to be shipped as a regular physical package. This method is attractive as it reduces the need for infrastructure compared to gaseous/liquid distribution. However, metal hydrides as hydrogen carriers are still very nascent.
Hydrogenation, the process that converts the carrier back to hydrogen, typically requires expensive catalysts and a lot of energy. What’s more, an estimated 30%-40% of energy is lost when hydrogen is converted from a gas to a liquid or a solid because hydrogen has a relatively low volume-to-energy density.
Where electrification is possible, hydrogen should not be considered as a viable energy source. In small- to medium-sized EVs and passenger vehicles, batteries will win out over fuel cells. Similarly, for domestic heating, electric heat pumps will win out over hydrogen heating systems and furnaces. Stay tuned for our report on electric heat pumps in Q4.
Anthony DeOrsey, Research Manager at Cleantech Group, discusses the innovators and trends we’re seeing in Heavy Industry Sustainability.
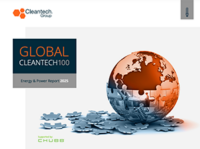