Industrial Heat Pumps Ready to Scale Up
Industrial heat is a major source of CO2 emissions, contributing to around 7 GT globally (around 20% of all emissions). While much of this comes from high temperature heat, such as process heat used in steel or concrete making, low temperature heat below 250°C is a major source of global CO2 emissions, accounting for around 7%. The good news is that much of this heat, especially in the dairy, food & beverage, and paper & pulp industries could already be decarbonized today.
Industrial heat pumps are emerging as a viable solution to electrify industrial heat, alongside electrical boilers, resistance heating, and biomass. The key selling point for industrial heat pumps is their superior efficiency – all competing technologies have efficiencies below 100%, while heat pump efficiency can reach up to 600% when operating with both heating and cooling cycles. While heat pumps are higher in CAPEX than competing technologies, including the incumbent gas boiler technology, the superior efficiency helps to bring down the payback period to as low as five years.
High power prices compared to natural gas, limited temperature range (80⁰-100⁰C), and limited consumer-side understanding have been some of the key reasons for slow adoption of industrial heat pumps, while high CAPEX, long integration times with significant plant downtime have acted as further deterrents to adoption.
Innovation Now Tackling Many of Those Pinch Points
Innovation focuses on increasing efficiency, performing bigger temperature lifts with higher efficiency, and reducing system installation and maintenance costs, with a focus on compressors, refrigerants, heat exchangers, and new heat pump designs.
Compressors consume up to 90% of the energy while compressor costs account for up to 40% of heat pump cost, so any efficiency gains will help improve overall system performance. Futraheat is developing a low maintenance centrifugal turbocompressor that can operate in high temperatures, reducing the need for maintenance and boosting the overall heat pump efficiency.
Traditional refrigerants, such as hydrofluorocarbons (HFCs) are harmful to the environment and struggle to reach temperatures over 100⁰C. Refrigerant costs are up to 15% of system cost. Exergyn is developing solid-state low GWP refrigerants from elastochloric material that could boost heat pump coefficient of performance (COP) – a measure of efficiency – to 20-25. QPinch is using a phosphor acid chemical loop as a refrigerant, which allows for higher temperature lifts while reducing moving parts.
Finally, new heat pump designs are combining heat pumps with energy storage (Green-Y), which allows the heat pumps to optimize their use of electricity from the grid. The designs that borrow from other waste heat technologies, such as Stirling engines, can operate across a range of different temperatures and waste heat source (Airthium).
Innovation Bolstered by Grant Financing
Industrial heat pump innovation has been well supported by a healthy grant environment in the U.S. and Europe for both R&D as well as adoption, with different subsidies available for facilities looking to swap out existing heating systems for heat pumps. This could further help to reduce the ROI to as low as 2-3 years. Meanwhile, venture capital into early-stage commercial heat pump innovation has been limited, as start-ups have access to non-dilutive grant financing. This has helped the start-ups to incubate their technologies to the early commercial stage. Founders often have pre-existing expertise from the heating and cooling sector, which has also helped to secure project financing.
One of the most notable examples of the non-dilutive financing is the $150M U.S. Department of Energy (DOE) grant to Skyven Industries to drive the deployment of the steam-generating heat pumps at manufacturing facilities in the US. This grant has to be matched with private funding, but it is still one of the largest grants made available to the high temperature heat pump industry and will help drive the adoption and understanding of industrial heat pumps.
A number of start-ups, such as Rank ORC and Skyven Technologies, have already commissioned commercially operating facilities. New business models, such as an energy-as-a-service (EaaS) model that does not require the customer to pay for CAPEX, and modular designs that allow for easy integration, have also made industrial heat pumps more attractive for customers.
Movement on the Policy Side
The European Emissions Trading System (EU ETS) will expand on small, combined heat and power (CHP) plants, which are mostly gas-fired, adding a carbon levy on facilities from 2027 onwards, facilitating switch away to cleaner technologies. The pressure to phase out fluorinated gases (F-gases) including hydrofluorocarbons (HFCs) – the main refrigerant in cooling systems – is increasing both in Europe as well as the U.S. When swapping out old equipment, heat pumps are likely to be a good solution.
There are still plenty of barriers to heat pump adoption, some of which may be harder to overcome than others, such as the lack of availability of grid connections and expensive grid fees. However, with the movement on the policy and innovation side, there are plenty of reasons to be bullish on industrial heat pumps.
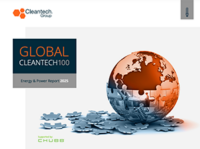