Innovation in Cathode Manufacturing: Enhancing Battery Efficiency and Sustainability
Lithium-ion batteries have gained substantial importance in the global energy transformation, playing a critical role in driving the adoption of electric vehicles (EVs) and the integration of renewable energy sources into the grid. At the core of these batteries is the cathode, composed primarily of metal oxides. This essential component significantly influences battery performance, energy density, and overall efficiency. Innovations in cathode manufacturing are a crucial step in enhancing battery efficiency and sustainability.
Challenges and Opportunities
The cathode materials market has experienced significant growth, with an estimated value of $29.5B in 2023. Projected to grow at an annual rate of 15.5%, it could potentially reach $70B by 2030. This growth underscores the sector’s significance and highlights the significant challenges it faces, particularly in the context of EVs. Cathode Active Materials (CAM), representing over 30% of the cost of EV batteries, present a significant hurdle to scaling the EV revolution.
Looking forward, the need for an additional 5 million tons of cathode active materials by 2032 raises concerns about resource sustainability. Continuing with current cathode production methods could lead to substantial water consumption of 20 billion gallons annually. Additionally, the dependence on China for 85% of the world’s refined battery materials exposes vulnerabilities within the supply chain, emphasizing the importance of diversification and robust supply networks.
Governments worldwide recognize the significance of cathode manufacturing innovation and its far-reaching implications for the energy landscape. In the U.S., the Bipartisan Infrastructure Law designates a substantial $7B to strengthen the domestic battery supply chain. This allocation supports upstream materials processing, a pivotal step in generating precursor materials for batteries.
Rethinking Cathode Manufacturing
Current cathode manufacturing processes are complex and resource-intensive, often involving the use of rare and hazardous materials. This approach leads to increased costs and substantial environmental consequences. This conventional approach is being challenged by innovative methodologies that prioritize process integration, resource efficiency, and reduced environmental impact.
- Morphology-Controlled Continuous Approach (Sylvatex): Introduces a continuous approach that reduces energy consumption, waste generation, and overall costs.
- High-Temperature Microwave Process (6K): Precisely tailors cathode materials to specific chemistry, size, and microstructure requirements, optimizing power and energy requisites while significantly reducing water consumption.
- Dynamic Crystallization (eJoule): Enables high-volume production rates and uniform production of high-capacity battery cathode materials. Currently deployed in a small-scale commercial plant with plans to expand to large-scale production.
In parallel, advancements in coating technologies and cathode material placement can complement new manufacturing processes. Atomic layer deposition (ALD) being commercialised by Forge Nano enables up to a 20% enhancement in performance. ALD precisely positions individual atoms, optimizing their arrangement to achieve superior capacity, safety, fast-charging capabilities, longevity, and cost-efficiency.
Figure 1: Simplified Comparison of Conventional Cathode Manufacturing and Innovative Approaches
Looking Ahead
Innovation in cathode manufacturing can enable a transition from complex and inefficient production processes to ones which are more resource-efficient and more environmentally friendly. However, their success will be shaped by the collaboration of industry stakeholders, scaling of manufacturing technologies, and policy actions.
- Development partnerships between innovators and battery manufacturers, such as 6K’s collaboration with ONE, helps to ensure market access and accelerates the adoption of innovative cathode materials.
- Governments will promote the adoption of innovative cathode materials and scaling of manufacturing. The U.S. has awarded only part of $7B allocated through the Bipartisan Infrastructure Law to strengthen the domestic battery supply chain.
- Impact will be achieved at scale with innovators including Sylvatex and 6K expecting to hit commercial scale of 10ktpa or above by around 2026.
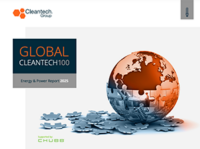