Thermal Energy Storage Innovation is Turning Up the Heat
Decarbonizing heavy industries will be one of the toughest nuts to crack for the next decade. Steel, cement, and iron combined account for over a fifth of global CO2 emissions and are notoriously difficult to decarbonize. Thermal energy storage (TES) can play a key role in decarbonizing these three sectors and other industries using high temperature heat.
Thermal energy storage (TES) is offering a new solution for decarbonizing heavy industries, such as steel, iron and cement. New materials and processes have enabled innovators to reach temperatures of over 1,000 degrees – the temperature range required to decarbonize hard-to-abate sectors, such as steel and cement, as well as power production. Lower temperature heat could be used in industrial applications, such as methanol or paper and pulp production, as well as in district heating.
TES systems use renewable power that is to be curtailed or sold to the market at a very low cost as an input, which is then stored by heating up materials with good thermal properties. It is not a new concept. Systems of concentrated solar power (CSP), which radiate heat to a receiver that uses molten salt, have existed for decades to transport and store electricity. In fact, there is a total of 6.8 GW of molten salt capacity installed across the world, but these technologies have historically been limited in temperature range and applications.
New Advanced Materials Progressing Innovation
Innovators have been experimenting with new materials, such as graphite, silicon and refractory brick. Stanford spin-out Antora Energy uses graphite as a heat storage conduit, in a system it refers to as a “giant toaster” and claims to reach temperatures of up to 1,500°C degrees. Thermal properties and performance of graphite are believed to improve when operating in high temperature environments.
Another U.S.-based innovator, Rondo Energy, uses refractory brick for storing heat, which has been used in the steel industry for years. Rondo recently achieved commercial temperatures of over 1,000°C in a test environment.
Kraftblock and Alumina Energy use different ceramic alloys to reach temperatures of 1,300-1,600°C. Newcomer MIT spin-out Electrified Thermal Solutions claims to reach heat of up to 1,800°C by using bricks, but the company is at a very early stage of its development. Kraftblock is already in the process of developing a 150 MWh thermal storage facility for food manufacturer Pepsico in The Netherlands to replace a 25 MW gas boiler.
Universities and national laboratories have played a key role in developing new high temperature materials and many are experimenting with further innovation. The NREL ENDURING project uses molten silicon to store up to 26 GWh of energy at 1,200°C.
The MIT Atomisic Stimulation and Energy Research Group is exploring a silicon heat battery that can reach a temperature of 2,400°C and use multi-junction photovoltaics to discharge to electricity. The lab in 2021 set the world record for the highest temperature liquid-metal pump at 2,082°C.
TES for Power Production
TES can also be used to store power. Renewable energy is stored as heat and converted back to power by using generators or heat exchangers in a power-to-heat-to-power (P2H2P) process when demand peaks or power prices are high. However, compared to competing long duration energy storage (LDES) technologies that can reach up to 90%, the roundtrip efficiency of the P2H2P process is only around 50%.
Still, TES is one of the very few solutions available for seasonal storage that spans for days or even weeks. Many innovators in the TES space do not consider power markets as their primary source of revenue but are open to receiving capacity payments for ad hoc power production as required by the TSO. Antora Energy, for example, plans to convert heat back into power by using a thermophotovoltaic process by radiating heat onto solar panels.
There are some innovators, however, that are oriented entirely for power production, such as molten salt developer Malta, CO2 battery innovator Energy Dome, and metal alloy TES company Azelio. The innovators argue that low roundtrip efficiency is irrelevant as input power is free as it would otherwise be curtailed or very low cost. Malta and Energy Dome also argue that they can achieve cost savings by using standard off-the-shelf components, such as turbines, generators and compressors.
TES for District Heating
The third key application for TES batteries is district heating. These solutions typically do not require very high temperatures and can operate in the range of 500-750°C. While power and industrial applications of TES are still in their nascency, commercial TES solutions in district heating are already operating.
Finnish developer Polar Night Energy commissioned the world’s first sand-based district heating system in Kankaanpää, Western Finland. The 8 MWh system provides Kankaanpää’s 12,500 inhabitants with heat for up to 80 hours.
Another Scandinavian innovator, Hyme, is building a 1 MW/20 MWh plant on the Danish Island of Bornholm. Following its commissioning in 2024, the molten salt system will provide heat, power and ancillary services for the local network.
Looking Ahead
At least nine advanced TES innovators have completed demonstration plants. We believe that the trickle of recent TES pilots will become a wave in 2023-2024, with commercialization likely within the next five years.
With very few incumbent solutions, innovators will compete against one another and sell into a blue ocean market. The innovations that reach for heat high enough to decarbonize industries are capable of heat ranges to generate power (>500°C), making TES a long-duration energy storage solution.
Anthony DeOrsey, Research Manager at Cleantech Group, discusses the innovators and trends we’re seeing in Heavy Industry Sustainability.
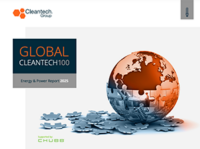