Will Photocatalysis Move the Needle on Chemical Carbon Emissions?
The chemical sector is the largest industrial energy consumer, using fossil fuels for both feedstock and energy use. Much of the latter occurs because reactions which turn feedstock into useful products typically rely on thermal catalysis. These processes often require relatively extreme reaction conditions, such as high temperatures and pressures. This results in reduced process efficiency and ultimately a substantial carbon footprint.
Alternative feedstocks such as waste, biomass, and CO2 can help the industry address fossil fuel use as feedstock. However, if the industry is to meet emissions reduction goals, a more energy efficient process will also be required. Conventional technologies have reached a high level of optimization which means the chemicals industry needs to address the emissions of fuel use. Carbon capture has scaled in recent years yet faces some challenges including cost and infrastructure, while using renewable energy can help reduce emissions, though costs are variable.
Photocatalysis offers a route to use renewable energy for chemical processing and increase process efficiency, and so it reduces emissions associated from fossil fuel use significantly – should the technology scale economically.
How Does Photocatalysis Work and What are the Benefits?
In photocatalysis, light energy is used to activate a catalyst which then accelerates a chemical reaction. Unlike in thermal catalysis, reaction rates have an exponential relationship with light intensity as well as temperature. This means that photocatalysis requires significantly lower temperatures than thermal catalysis for required reaction rates.
The theoretical benefits of photocatalysis were the focus of research by scientists at Rice University which developed plasmonic photocatalysts which can drive chemical reactions with high photocatalytic efficiency, selectivity, and specificity. The technology was then licenced to Syzygy Plasmonics that developed ‘photoreactors’ which use LEDs to illuminate photocatalysts, which catalyze reactions. The reactors are made from relatively inexpensive materials which helps to keep capital costs low. Meanwhile, the process benefits from high efficiency, selectivity, and specificity resulting in reduced energy use, resulting in lower costs and a reduced carbon footprint.
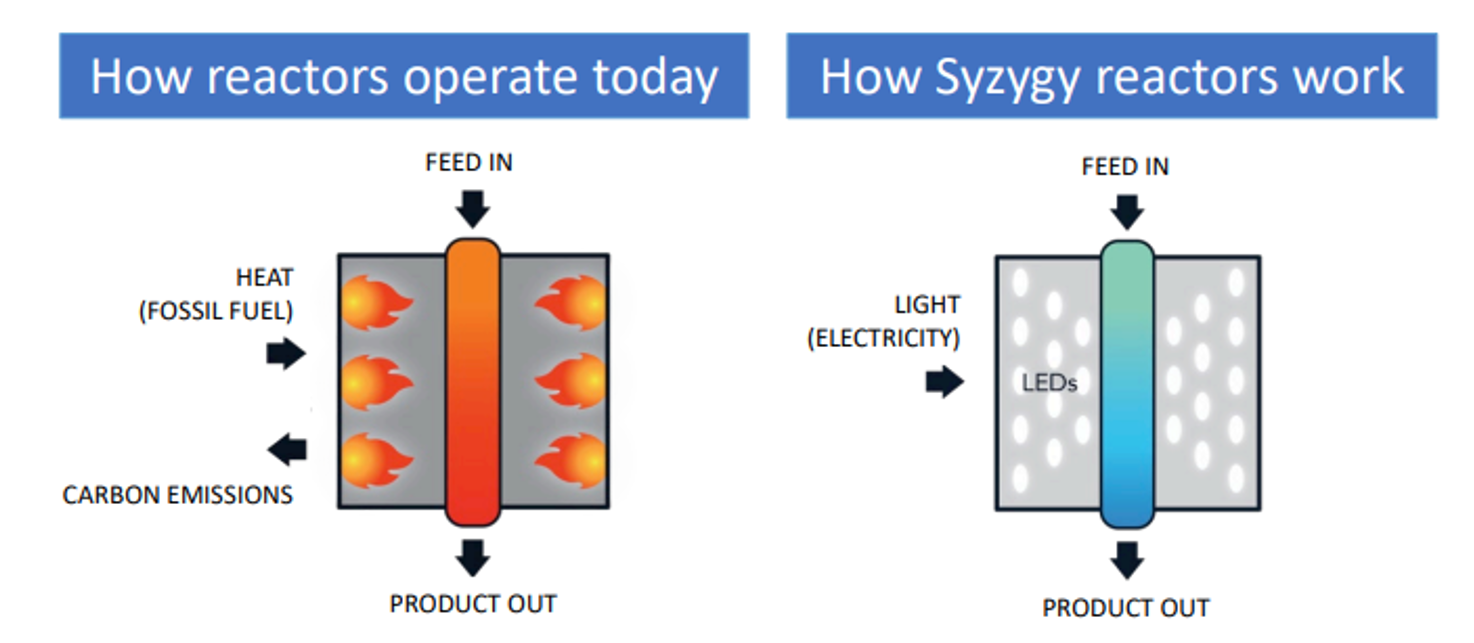
The Potential for Impact
Syzygy Plasmonics has developed the technology for several applications including decomposition (cracking) of ammonia. Currently produced in large volumes for fertilizer, ammonia is increasingly recognized as a promising hydrogen carrier – useful as both a transportation fuel and for energy imports. However, the roundtrip efficiency (and cost) of ammonia production and decomposition remains a barrier for adoption. When deployed at scale, Syzygy’s technology promises far greater efficiency than thermal cracking, opening the possibility of displacing natural gas imports with clean ammonia imports.
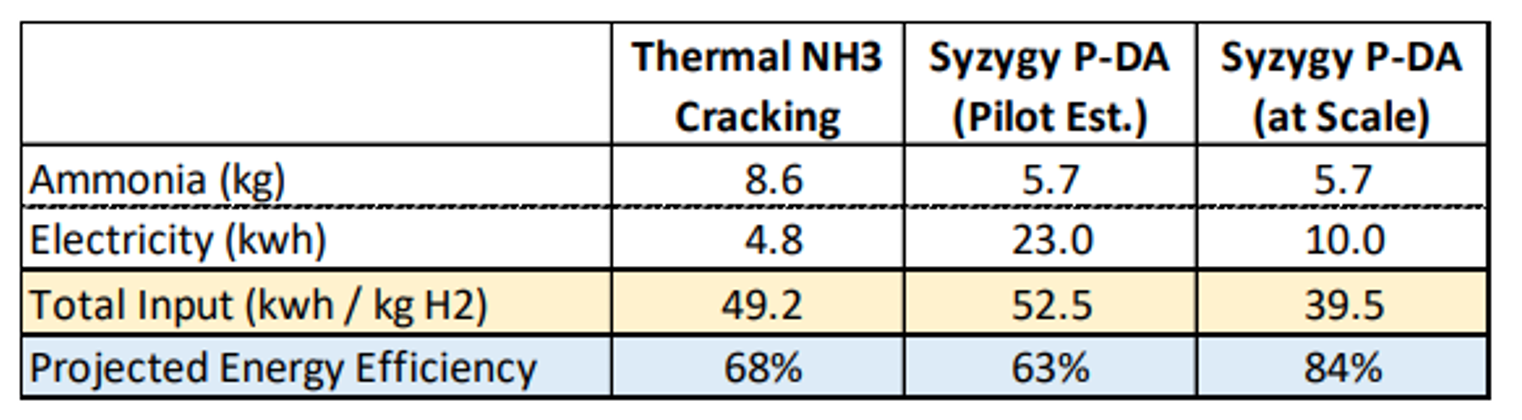
Other approaches for energy import exist, and ammonia compares especially favorably with other hydrogen carriers such as methanol where access to carbon sources is constrained. The amount of ammonia that will be converted back into hydrogen for energy or industrial use is dependent on many variables. 100-130Mt of hydrogen by 2050 would align with IEA estimates for nitrogen demand for energy use, but this could be direct use or hydrogen. If it were all cracked, using Syzygy technology in place of thermal cracking would save around 1000-1250TWh of energy – around 3 times the annual total energy use of the UK.
The technology is unlikely to be deployed at scale unless it competes on total cost compared to other technologies. However, the efficiencies are expected to drive costs lower with Syzygy expecting the technology to reduce total costs associated with ammonia cracking by over 20% compared to thermal cracking, though the cost competitiveness will depend on costs of renewable energy.
Looking Forward
Syzygy has an ammonia cracking pilot under development with Lotte Chemicals, while the potential to scale will be reaffirmed with Syzygy demonstrating efficiencies at scale. The technology has also been tested for several applications including steam methane reforming (for producing hydrogen), and dry methane reforming (for producing syngas which can be used in production of methanol or jet fuel). Many other applications exist including technology for ammonia synthesis, green hydrogen, ethylene, and aromatics synthesis, with potential to save gigatons of carbon emissions.
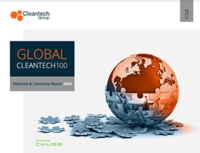